This page describes the process flow used to produce NFK products and deliver them to users as rapidly as possible.
01.Rolling sheet steel to create pipes
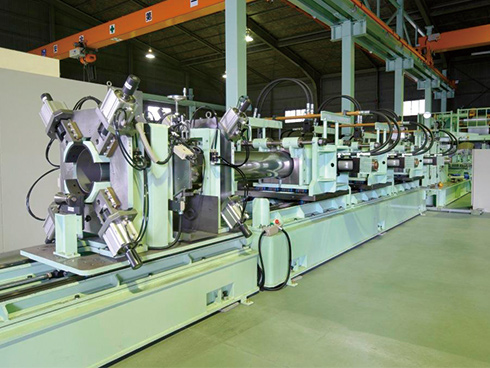
Creating the pipe (tube element) is the most important process in creating flexible hoses and expansion joints.
NFK has a pipe maker for creating flexible hoses of 3 to 350 mm in diameter, and a pipe maker for creating expansion joints of 20 to 2,800 mm in diameter.
02.Forming tubes with forming machine
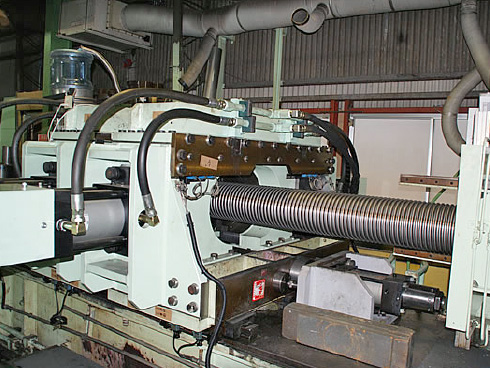
Three forming methods are used.
- Roll forming
– A special wheel is used to form corrugations on the pipe. - Bulge forming (elastomeric forming)
– Pressure is applied to a special resin from the inside of the pipe, and the force of its expansion is used to form corrugations. - Liquid-pressure forming (hydroforming)
– A method similar to bulge forming that uses a liquid (such as water or oil) instead of a special resin to form corrugations.
03.Weaving wire braiding using braiding machine
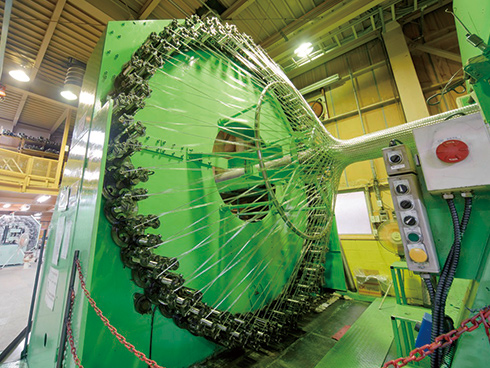
Wire braiding (woven stainless steel wires) is a component that increases the pressure resistance and strength of flexible hoses.
Wire braiding made using a braiding machine is mounted on the outside of flexible hoses.
04.Cutting tubes to production length
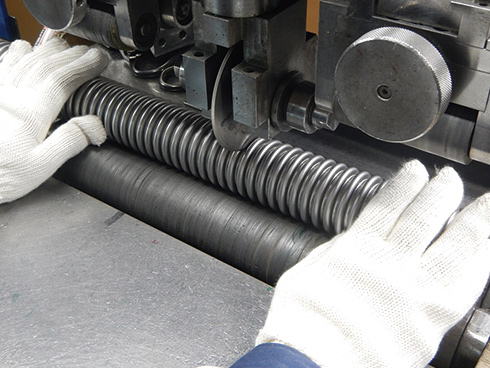
Flexible hoses are cut to the specified length as specified by the client’s order.
05.Attaching joints
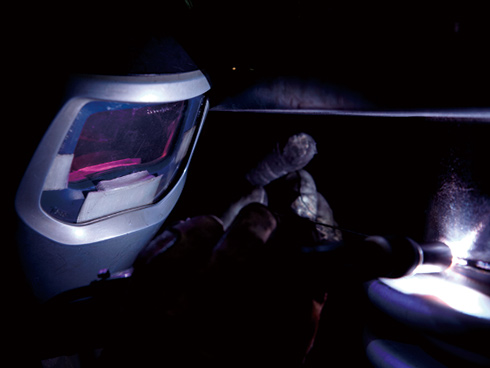
There are two methods of attaching joints to flexible hoses or expansion joints.
- Welding
– Joint types such as flange joints and screw joints can be attached to flexible hoses and expansion joints by welding. - Crimping
– Joint types such as flange joints and screw joints can be crimped with a special crimping machine and attached via a special connector.
06.Testing
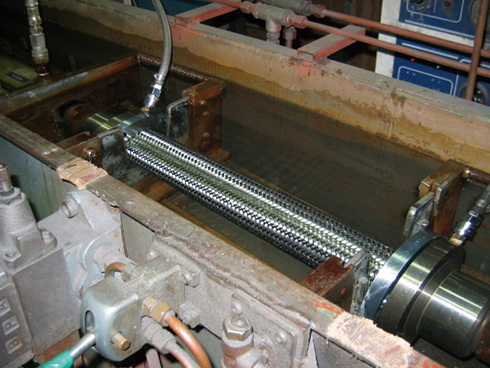
All flexible hoses and expansion joints are leak tested.
- Immersion-type airtightness test method
– Air is pumped into the product to pressurize it. The product is then immersed in that state and leakage is checked for by examining whether bubbles appear. - Non-destructive inspection
– Non-destructive inspections are used to check the solidity of welds of difficult-to-immerse parts such as large-diameter expansion joints.
07.Drying
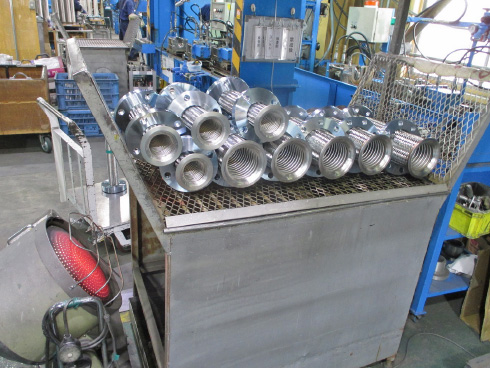
Water or other liquids must not remain inside products.
Products are dried by warming them to evaporate remaining moisture, or pumping warm air into the product.
08.Shipment
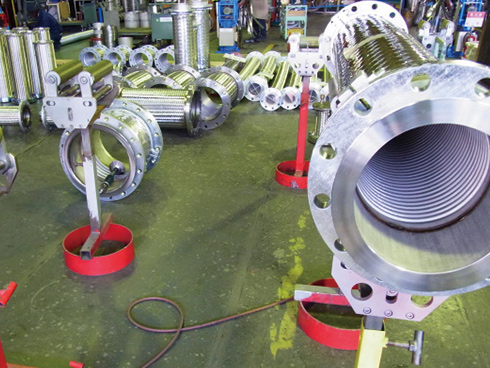
Processes from packaging to shipment also affect product quality.
Suitable packaging is used to prevent damage to products during shipment, ensuring products reach users in the optimum state.